Aluminum Alloy Quality Testing | HXM
Aluminum alloys are widely used in various industries due to their excellent properties such as light weight, durability and corrosion resistance. However, ensuring their quality is essential to meet application requirements and achieve optimal performance. In order to ensure product quality and deliver perfect aluminum alloy products to customers, we meet any testing requirements of customers in terms of aluminum alloy quality inspection.
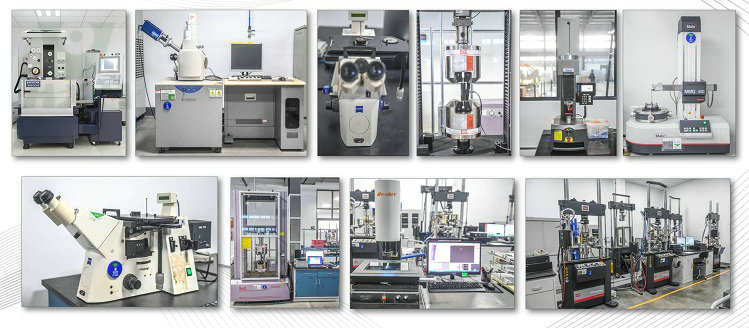
Aluminum Alloy Quality Testing Methods
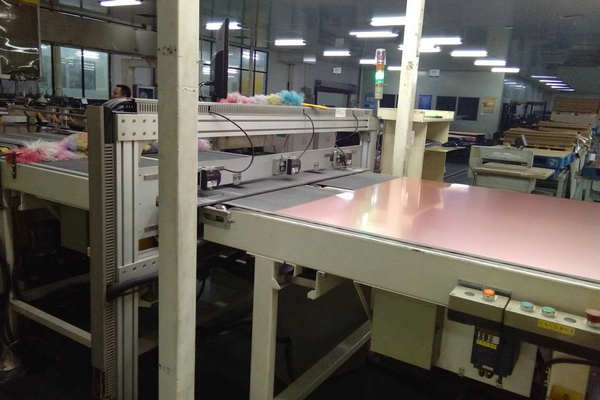
Appearance Inspection
The quality of the surface of aluminum alloy products is an important basis for judging whether they meet the standards. The main inspection contents are as follows:
Surface Finish: Whether there are scratches, cracks, dents, or bubbles.
Oxide Film Quality: Whether it is uniform, without falling off, spots, or discoloration.
Dimensional Accuracy: Whether the length, width, thickness, roundness, etc. meet the standard requirements.
Flatness: Whether there is obvious bending or warping of the plate.
Chemical Composition Detection
The chemical composition of aluminum alloy directly determines the performance of the material. The following methods are usually used for detection:
Spectrometer: Rapidly detect the content of the main elements (such as silicon, magnesium, zinc, copper, etc.) in aluminum alloy.
Chemical Titration: Used to detect the content of certain specific elements.
Composition Comparison: Ensure that the composition meets international standards (such as ASTM, EN, etc.) or customer specifications.
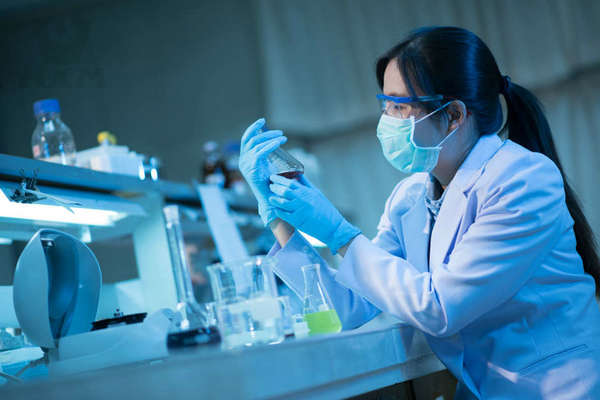
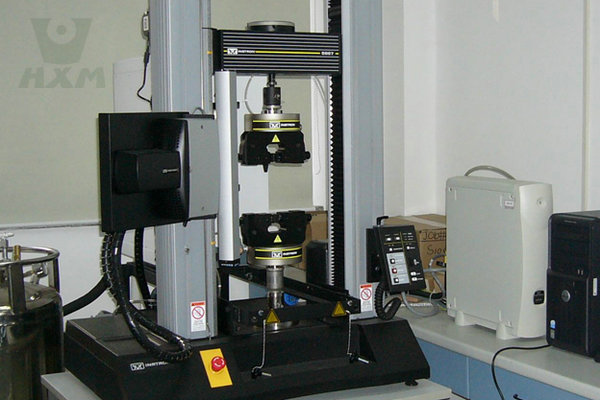
Mechanical Properties Testing
Mechanical properties are key indicators of whether aluminum alloys can meet the requirements of use, usually including:
Tensile Strength: The maximum tensile force that the material can withstand in a tensile test.
Yield Strength: The maximum stress that the material can withstand without permanent deformation.
Elongation: The degree of plastic deformation after breaking after stretching.
Hardness: Use Brinell hardness (HB) or Vickers hardness (HV) to test its compressive strength.
Metallographic Inspection
Observe the internal structure of aluminum alloy through a microscope to determine whether the size and distribution of grains are uniform and whether there are:
Porosity or Inclusions: Defects inside the material.
Segregation: Problems with uneven distribution of components.
Grain Boundary State: Whether the grain boundary is clear and whether there are cracks.
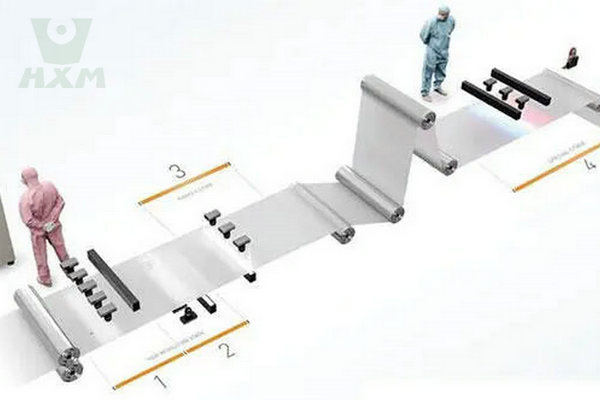
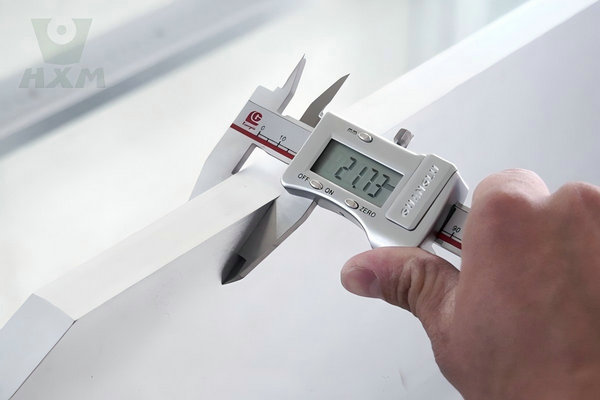
Dimension and Geometric Accuracy Inspection
Ensure that the shape and size of aluminum alloy products meet customer requirements, the main contents include:
Thickness Deviation: Detect the thickness of plates, films, or profiles.
Tolerance Range: Whether it is within the specified range, such as diameter deviation, length tolerance, etc.
Edge Neatness: Ensure that there are no burrs on the edges after cutting or processing.
Surface Coating Inspection
If the aluminum alloy product has a coating or anodizing treatment, the coating quality inspection is required:
Coating Thickness: Whether it meets the anti-corrosion or decoration requirements.
Coating Adhesion: Whether the coating is firm and not easy to peel off.
Corrosion Resistance: Evaluate the anti-corrosion effect of the coating through salt spray tests or other methods.
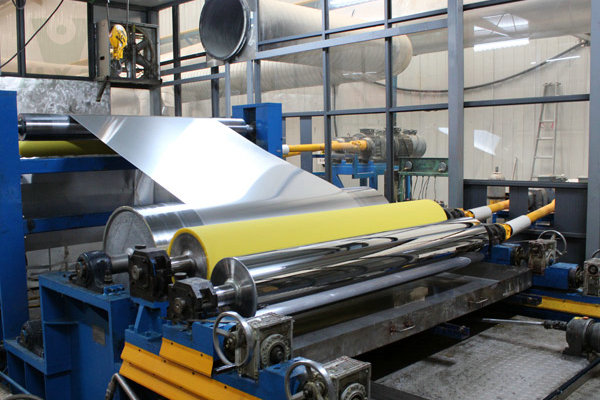
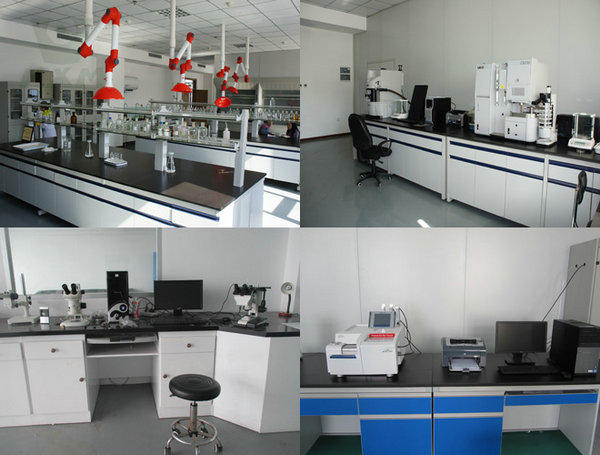
Process Performance Inspection
Depending on the application, the processing performance of aluminum alloy may need to be tested:
Weldability: Evaluate whether the aluminum alloy is suitable for the dying process.
Formability: Check whether the material can meet the requirements of stamping, bending, or other processing.
Heat Resistance: Whether it maintains strength and stability under high-temperature conditions.
Special Performance Testing
For some aluminum alloy products with special purposes, additional performance checks may be required:
Electrical Conductivity: Aluminum alloys used in the power industry need to measure electrical conductivity.
Thermal Conductivity: Aluminum alloys used in heat dissipation devices need to test thermal conductivity.
Corrosion Resistance: Aluminum alloys used in marine environments or chemical devices need to undergo corrosion testing.
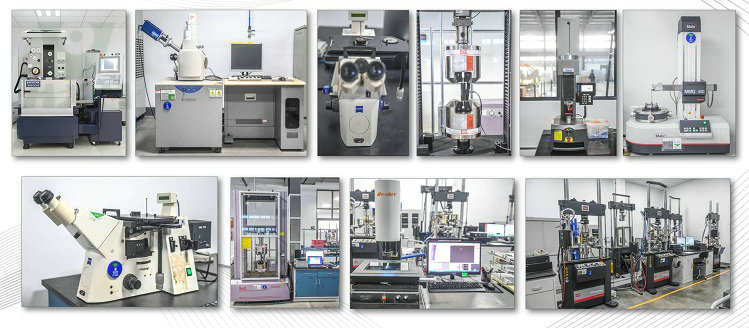
Looking forward to being your Metal choice!