5056 Aluminum Bar Supplier In China
We specialize in providing high-quality aluminum bars to meet a variety of industrial needs. 5056 is an Al-Mg anti-rust type aluminum alloy, which cannot be strengthened by heat treatment. In addition to the low manganese content, the chemical composition of the alloy is similar to that of the 5B05 alloy, of which the magnesium content is slightly higher than that of the 5A05 alloy, and the properties are similar to that of the 5B05. The alloy has good plasticity in the annealing state, its corrosion resistance is good, and the weldability is acceptable.
Huaxiao Metal is a leading 5056 Aluminum Bar Supplier in China, dedicated to providing high-quality aluminum bars to customers worldwide. As an experienced 5056 Aluminum Bar Manufacturer, we have advanced production equipment and a strict quality control system to ensure that every aluminum bar meets international standards.
Contact us now to learn more about 5056 aluminum bars stock and prices.
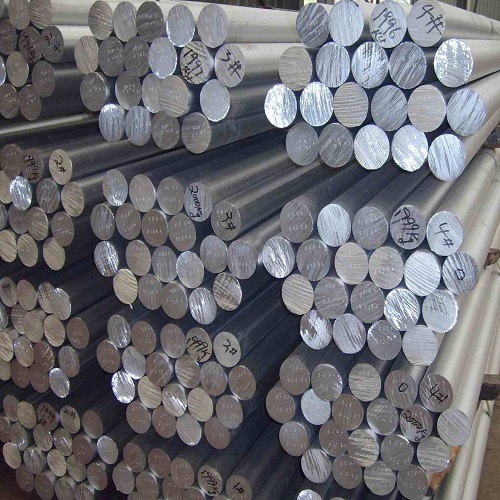
5056 Aluminum Bars Specifications
Standards: ASTM B221, B211, B565, B316
Aluminum bar form: Aluminum round, hexagonal, flat, semi-circular, oval, rectangular black, and glossy finish
Aluminum round bar diameter: 0.1-600mm, etc.
Aluminum hexagonal bar: 0.1-600mm, etc.
Aluminum angle bar size: 0.5mm*40mm*40mm-20mm*400mm*400mm
Aluminum flat steel thickness: 0.1-600mm, etc.
Aluminum flat bar size: 1-2500mm, etc.
Aluminum round bar length: 1-12m, random, fixed, and cut length or according to customer requirements
Temper: H32, H34, H36, H38, etc.
5056 Aluminum Bars Data Sheet - China Manufacturer
Chemical Composition
Al | Si | Fe | Cu | Mn | Cr | Mg | Mn+Cr | Ti | Zn | Other Each | Others Total |
AL 5056 | 0.3 max | 0.4 max | 0.10 max | 0.05/0.20 | 0.05 / 0.20 | 4.50 / 5.6 | – | – | 0.10 max | 0.05 each | 0.15 max |
Mechanical Properties
Mechanical Properties | Details |
---|---|
Brinell Hardness | 50-60 HB |
Weldability | Good |
Fatigue Resistance | Excellent |
Contact Huaxiao Metal now to get 5056 Aluminum Bar Prices, Stock Availability, and detailed specifications information. We look forward to cooperating with you and becoming one of your trusted 5056 Aluminum Bar Supplier!
Physical Properties
Physical Properties | Details |
---|---|
Density | 2.66 g/cm³ |
Melting Point | 607-640°C |
Elastic Modulus | 70-80 GPa |
Electrical Conductivity | 33% IACS |
Thermal Expansion Coefficient | 24.2 µm/m·°C (20°C – 100°C) |
Thermal Conductivity | 130 W/m·K |
Tensile Strength | 230-275 MPa |
Yield Strength | 110-200 MPa |
Elongation | 10-20% |
We offer 5056 Aluminum Bar Stock in a variety of specifications and sizes to meet the needs of different industrial fields. If you need detailed specifications or customized services, please consult the 5056 aluminum bar price.
5056 Aluminum Bar Packages
The following is our company’s standard aluminum bar export packaging. If the customer has any packaging requirements, our company can meet them.
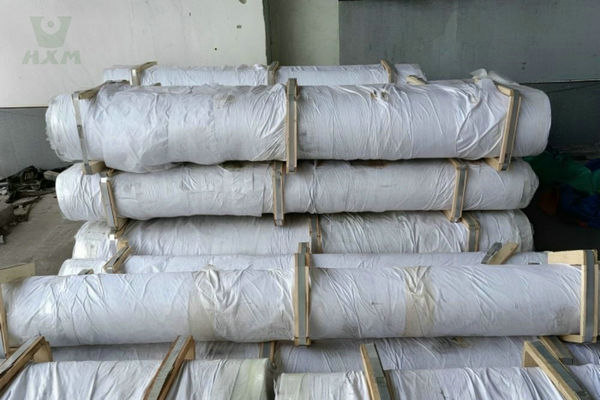
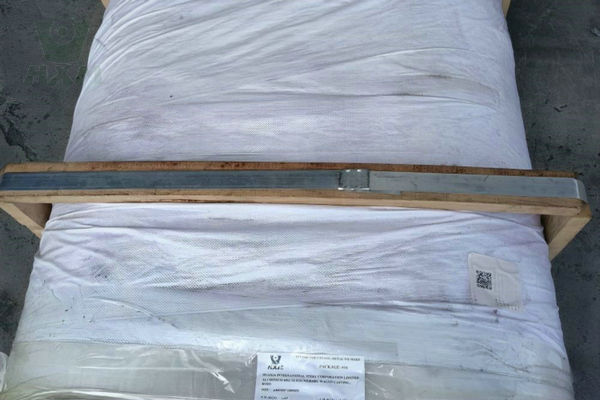
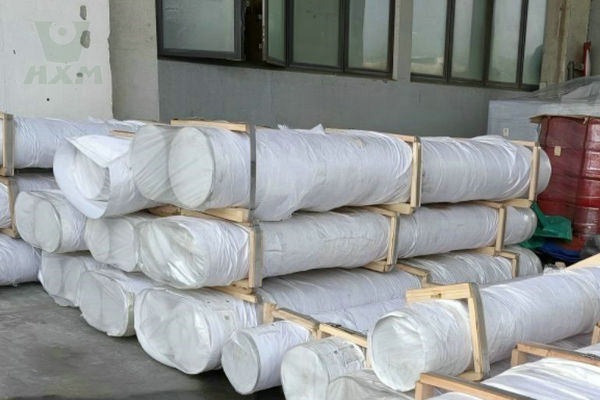
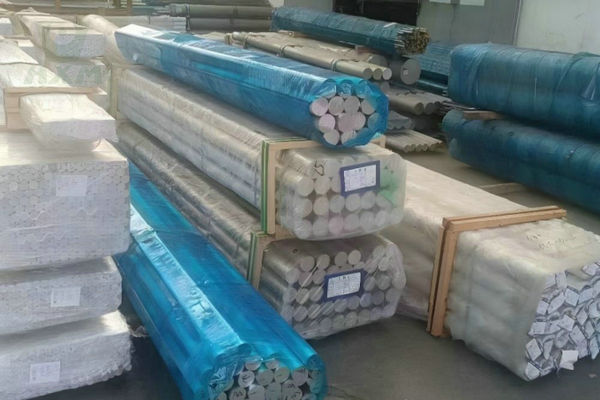
FAQ
What is 5056 Aluminum Bar?
5056 aluminum bar is an aluminum material made of 5056 aluminum alloy, which has excellent corrosion resistance and medium strength. 5056 aluminum alloy belongs to the aluminum-magnesium alloy family, contains about 5% magnesium, and is widely used for its high strength, fatigue resistance and good processing properties. It is often used to manufacture structural parts and components in aerospace, automobiles and marine environments, because in these applications, corrosion resistance and lightweight are very important.
https://www.hxm-aluminum.com/products/5000-series-aluminum.html
Main Features of 5056 Aluminum Bar
Corrosion Resistance: This is especially suitable for use in corrosive environments such as moisture and salt water.
Strength: Compared with other aluminum alloys, 5056 aluminum has medium strength and is suitable for a variety of structural applications.
Processability: Easy to cut, weld, and form, suitable for various manufacturing processes.
Fatigue Resistance: Suitable for applications that need to withstand repeated loads.
Applications of 5056 Aluminum Bar
Alloy 5056 is commonly used to rivet aluminum alloy and magnesium alloy assemblies. There is also 5056 coated aluminum wire, which is widely used in the production of window screens and other wire products that require good corrosion resistance.
Aerospace industry
Shipbuilding and marine engineering
Automobile manufacturing
Some building materials and decorative materials
Is 5056 Aluminum Bar Suitable for Welding?
Yes, 5056 aluminum alloy is suitable for welding, especially common welding techniques such as MIG (gas metal arc welding) and TIG (tungsten inert gas arc welding). The presence of magnesium enhances the weldability of 5056 aluminum and is less prone to cracking during welding.
Welding Characteristics of 5056 Aluminum Alloy:
Good weldability: 5056 aluminum is suitable for most standard welding methods, especially gas-shielded welding (MIG, TIG).
Post-weld treatment: After welding, the strength of the heat-affected zone (HAZ) may be reduced. Depending on the specific application, post-weld heat treatment or annealing may be required to restore some strength.
Corrosion resistance: Welding has little effect on the corrosion resistance of 5056 aluminum, so it is still suitable for use in marine or other corrosive environments.
Welding Recommendations:
Filler material: It is recommended to use similar filler materials such as 5356 aluminum alloy to maintain strength and prevent cracking during welding.
Shielding gas: Argon or argon-helium mixtures are usually used as shielding gas when welding 5056 aluminum.
5056 Aluminum Bars Compared to Other Aluminum Alloys?
5056 Aluminum Bar vs. 6061 Aluminum Bar
Property | 5056 Aluminum Bar | 6061 Aluminum Bar |
---|---|---|
Primary Alloying Element | Mg | Mg and Si |
Strength | Moderate | Moderate to High |
Corrosion Resistance | Excellent, especially in marine environments | Good, suitable for various environments |
Machinability | Good | Excellent, easy to machine and form |
Weldability | Good | Excellent, widely used in welded structures |
Applications | Marine, outdoor equipment, and structures | Industrial frames, building structures, automotive, and aerospace components |
5056 offers better corrosion resistance, especially in marine environments, while 6061 has superior machinability and weldability with higher overall strength, making it ideal for industrial and structural applications.
6061 Aluminum Bars
5056 Aluminum Bar vs. 7075 Aluminum Bar
Property | 5056 Aluminum Bar | 7075 Aluminum Bar |
---|---|---|
Primary Alloying Element | Mg | Zn, Cu, and Mg |
Strength | Moderate | Very high, near steel-like strength |
Corrosion Resistance | Excellent | Poor, susceptible to stress corrosion |
Machinability | Good | Good but more brittle |
Weldability | Good | Poor, prone to cracking during welding |
Applications | Marine, outdoor equipment, and structures | Aerospace, high-strength mechanical components |
7075 offers exceptional strength, widely used in aerospace and high-performance mechanical components. However, it has poor corrosion resistance and weldability, making 5056 a better choice for marine and outdoor applications where corrosion resistance is critical.
7075 Aluminum Bars
5056 Aluminum Bar vs. 5083 Aluminum Bar
Property | 5056 Aluminum Bar | 5083 Aluminum Bar |
---|---|---|
Primary Alloying Element | Mg | Mg and Mn |
Strength | Moderate | High, especially in applications requiring tensile strength |
Corrosion Resistance | Excellent, especially in marine environments | Excellent, ideal for marine and chemical environments |
Machinability | Good | Good, suitable for large-scale processing |
Weldability | Good | Excellent, suitable for most welding methods |
Applications | Marine, outdoor equipment, and structures | Shipbuilding, chemical tanks, pressure vessels |
Both 5056 and 5083 offer excellent corrosion resistance, but 5083 has higher strength, making it better suited for applications like shipbuilding and pressure vessels. 5056, with its moderate strength, is more appropriate for lighter-duty marine structures.
5083 Aluminum Bars
5056 Aluminum Bar vs. 2024 Aluminum Bar
Property | 5056 Aluminum Bar | 2024 Aluminum Bar |
---|---|---|
Primary Alloying Element | Mg | Cu |
Strength | Moderate | High strength |
Corrosion Resistance | Excellent | Poor, susceptible to corrosion in humid environments |
Machinability | Good | Good |
Weldability | Good | Poor, prone to cracking during welding |
Applications | Marine, outdoor equipment, and structures | Aerospace, military, high-stress parts |
2024 offers high strength but poor corrosion resistance, especially in humid or corrosive environments. 5056 is better suited for marine or outdoor environments where corrosion resistance is a priority, while 2024 excels in aerospace and high-stress components.
2024 Aluminum Bars