A5056 is a magnesium-based aluminum alloy, also known as A5000. This article will introduce the characteristics and applications of A5056 aluminum.
What is A5056?
A5056 is an aluminum alloy with about 4.5-5.6% magnesium added to aluminum. Due to the high magnesium content, its corrosion resistance and strength are improved. It also has high machinability and good welding properties. As an aluminum alloy, it is not too soft or too hard and is an easy-to-process material. It is usually circulated in the market as round bars and is widely used as an aluminum alloy round bar. The processing methods of round bars are mainly extrusion or drawing.
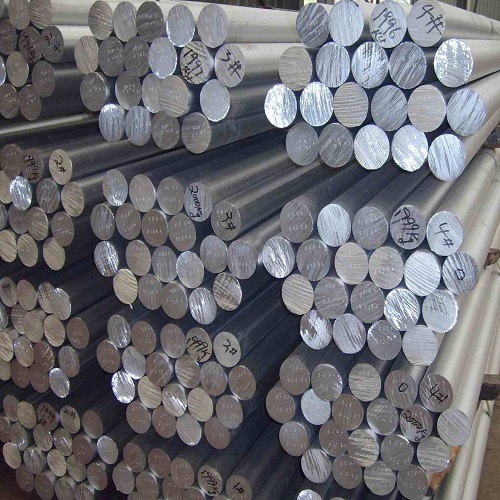
Features of A5056
Lightweight is one of the characteristics of aluminum alloy. In addition, A5056 has many other advantages. The following are its typical advantages and disadvantages.
Advantages of A5056 Aluminum
- Excellent corrosion resistance
- Excellent formability
- Good surface finish after cutting
- Good anodizing
Aluminum and magnesium are both metals that easily form oxide films on the surface. In particular, the oxide film formed on the surface of aluminum is a non-dynamic film that has the effect of resisting metal corrosion. Therefore, A5056 is also a corrosion-resistant metal material with an oxide film on the surface. In addition, the high magnesium content also gives this material a certain strength and good formability, which is suitable for forming processes such as extrusion and drawing. In addition, due to its moderate hardness, it also has high machinability, and the surface is smooth and beautiful after cutting. It is also suitable for anodizing, and the corrosion resistance and decorativeness can be improved through anodizing.
Disadvantages of A5056 Aluminum
- The surface is easy to scratch
- Cannot be used in parts that require higher strength
Although its strength is higher than pure aluminum or A5052, as a metal, it is still not a particularly strong metal. Therefore, the surface is likely to be dented and scratched due to collisions, scrapes, and sliding. If such scratches occur frequently, the oxide film will also be damaged, resulting in reduced corrosion resistance. It is also not suitable for use in places where high strength is required. Due to its low specific gravity, it is often used in machine parts to reduce the overall weight, but care must be taken in the use area.
Application of A5056 Aluminum
A5056 is widely used as a round bar, but it is also used in many other processes in our daily lives. Because of its good cutting surface finish, it is often used to make parts that are easily visible to the public. Here are the main uses of A5056.
- Electronic components
- Optical instruments
- Rivets
- Industrial zippers
- Wire for wire mesh
- Honeycomb core
As a lightweight and easy-to-process material, it is often used for parts of electronic equipment, etc. For the same reason, it can also be used in optical components such as camera lens bodies. Rivets and industrial zippers, wire for wire mesh, etc. are examples of applications that take advantage of their good formability and high corrosion resistance. In addition, the honeycomb core takes advantage of its lightweight and high thermal conductivity. Because of its wide range of uses, this material is also called a general-purpose aluminum alloy round bar.
Differences between A5056 and other Materials
A5056 is a magnesium-based aluminum alloy that belongs to the A5000 series along with A5052, which is known as general-purpose aluminum. Another material that is also widely used in the industrial field is duralumin. This section will introduce the differences between general-purpose aluminum, duralumin, and other metals.
Differences from Duralumin Alloys
Duralumin alloys are also a type of aluminum alloy. They refer to materials that are mixed with additives such as copper in aluminum. There are three types: A2017 (duralumin alloy), A2024 (super duralumin alloy), and A7075 (super duralumin alloy). Duralumin is characterized by high strength, so the strength of these three aluminum alloys is higher than that of A5056. On the other hand, A5056 is better in corrosion resistance and weldability than duralumin. Since A5056 is mainly circulated in the form of round bars, it is often processed by turning.
However, it is often difficult to perform continuous processing because the chips easily stick together. In particular, when performing automatic processing using CNC, the machine tool must be stopped at the right time to remove the chips. This sometimes increases the processing time. In addition, compared with A5056, hard aluminum alloy materials are easier to cut continuously because their chips are intermittent. Therefore, although the material cost is higher, the processing time is reduced, which in many cases will reduce costs.
Differences with A5052 Aluminum
A5056 and A5052 are two common magnesium-based aluminum alloy materials. The magnesium content in A5052 is about 2.2% to 2.8%, while the magnesium content in A5056 is about 4.5% to 5.6%. Therefore, A5056 has higher strength and moderate hardness, so it is more suitable for cutting and forming.
On the other hand, its weldability is poor, so special attention is required. It is usually welded with A5052. In addition, A5056 also has better anodizing performance, so it is suitable for manufacturing parts that require decorative and visible parts. It has a variety of circulation forms, and a honeycomb core is one of them. Although it has a large circulation in round rod form, it is still different from A5052, which is mainly circulated in sheet form.
Differences with Stainless Steel and Iron
The specific gravity of A5056 is 2.64, which is a very light metal compared with 7.9 of S45C and 7.7 of SUS430. However, it should be noted that its strength is only about half of that of stainless steel and iron. Compared with iron, it is a relatively soft material and is easier to cut. On the other hand, its high thermal conductivity means that heat tends to overflow from the parent material during welding, resulting in poor weldability.
In Conclusion
A5056, also known as a general aluminum alloy round bar, is a type of magnesium aluminum alloy. This material is lightweight and highly corrosion resistant, making it suitable for machining such as cutting and forming. It can be used in a wide range of applications, such as optical equipment, rivets, and wire for wire mesh.
Although it is slightly better weldable than A5052, it is not as good as steel or stainless steel and is also difficult to weld. However, it is suitable for anodizing, can also be color anodized, and is used for parts that are easily visible to the public. It is mainly circulated in the form of round bars through extrusion and drawing.