Aluminum alloys are highly versatile and widely used in various industries, but not all alloys are created equal. Two popular options are 5052 aluminum vs 6061 aluminum. While both are excellent materials, they differ significantly in chemical composition, mechanical properties, corrosion resistance, and applications. This article provides a detailed comparison to help you choose the right alloy for your needs.
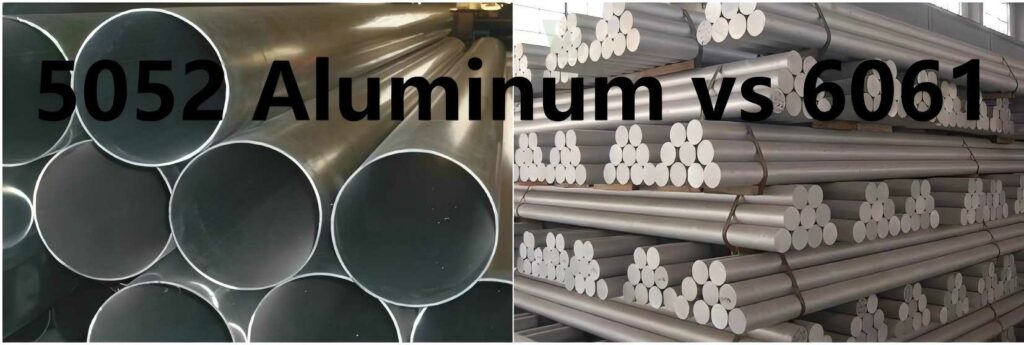
What is 5052 Aluminum Alloy?
5052 aluminum alloy is a non-heat-treatable alloy primarily made of magnesium. It is highly valued for its outstanding corrosion resistance, especially in marine environments, and its high fatigue strength. This alloy is commonly used in industries like shipbuilding, automotive, and pressure vessels.
Key features of 5052 aluminum:
- Superior corrosion resistance
- Excellent formability
- High fatigue strength
- Non-heat-treatable
What is 6061 Aluminum Alloy?
6061 aluminum alloy is a heat-treatable alloy primarily composed of magnesium and silicon. Known for its exceptional mechanical properties and excellent corrosion resistance, it is a top choice in industries such as aerospace, automotive, and construction. Its high strength-to-weight ratio and versatility make it one of the most commonly used aluminum alloys.
Key features of 6061 aluminum:
- High strength and stiffness
- Good weldability and machinability
- Excellent corrosion resistance
- Heat-treatable for enhanced properties
5052 Aluminum vs 6061 Aluminum: What's the Difference
Composition of 5052 Aluminum VS 6061 Aluminium
Element | 5052 Aluminum (%) | 6061 Aluminum (%) |
---|---|---|
Al | Balance | Balance |
Mg | 2.2 – 2.8 | 0.8 – 1.2 |
Si | 0.25 max | 0.4 – 0.8 |
Cr | 0.15 – 0.35 | 0.04 – 0.35 |
Fe | 0.4 max | 0.7 max |
Cu | 0.1 max | 0.15 – 0.4 |
Zn | 0.1 max | 0.25 max |
Mn | 0.1 max | 0.15 max |
Mechanical Properties of 5052 Aluminum VS 6061 Aluminium
Property | 5052 Aluminum | 6061 Aluminum |
---|---|---|
Tensile Strength (MPa) | 193 – 228 (H32 temper) | 290 – 310 (T6 temper) |
Yield Strength (MPa) | 89 – 121 (H32 temper) | 241 – 276 (T6 temper) |
Elongation at Break (%) | 5 – 12 | 8 – 12 |
Fatigue Strength (MPa) | 123 | 96 |
Hardness (Brinell HB) | 60 | 95 |
Modulus of Elasticity (GPa) | 70 | 68 |
The data provided by different aluminum alloy manufacturers may be slightly different. If you are looking to purchase aluminum alloy, please contact us and tell us your needs. We will meet your requirements!
5052 vs 6061 Aluminum Tempers
Both alloys are available in various tempers.
- 5052 is commonly found in H32 and H34 tempers for improved strength.
- 6061 is often available in T6 and T651 tempers for optimal strength and machinability.
5052 vs 6061 Aluminum Weight
Both alloys have similar densities, but their application-specific designs may affect overall weight.
Corrosion Resistance Properties Of 5052 vs. 6061 Aluminum
- 5052: Superior in saltwater and marine environments.
- 6061: Provides excellent resistance to general corrosion but is less effective in highly acidic or saline conditions.
Weldability Properties Of 5052 And 6061 Aluminum
- 5052: Exceptional weldability, especially for marine and automotive components.
- 6061: Good weldability, but heat treatment may be required after welding to restore properties.
5052 vs 6061 Aluminum Alloy Heat Treatment
- 5052: Non-heat-treatable; strength is achieved through cold working.
- 6061: Heat-treatable, with T6 temper offering maximum strength.
Formability of 5052 Aluminum VS 6061 Aluminum
- 5052: Highly formable, suitable for bending and shaping.
- 6061: Less formable but excels in applications requiring machining.
Fatigue Strength of 5052 Aluminum VS 6061 Aluminum
- 5052: Higher fatigue strength, making it better for dynamic loads.
- 6061: Moderate fatigue strength, ideal for structural stability.
Workability of 5052 Aluminum VS 6061 Aluminum
- 5052: Easier to work with due to its malleability.
- 6061: Requires more effort in machining but provides excellent results.
Cost of 5052 Aluminum VS 6061 Aluminum
- 5052: Generally more affordable due to its simpler production process.
- 6061: Slightly more expensive because of its enhanced mechanical properties and heat treatment.
Applications of 5052 Aluminum Vs 6061 Aluminum
- 5052 aluminum: Marine parts, fuel tanks, pressure vessels, signage.
- 6061 aluminum: Aircraft components, automotive frames, construction structures, bicycles.
Still unsure? Reach out to Huaxiao Metal’s technical team for free alloy selection consultation based on your industry!
Similarities Between 5052 and 6061 Aluminum Alloys
Despite their differences, both alloys share some similarities:
Lightweight and corrosion-resistant
Excellent for welding and machining
Widely available in multiple forms
Need help choosing? Contact us to get expert advice and pricing today.
FAQ: 5052 Aluminum vs 6061 Aluminum Alloy
Which aluminum alloy is easier to weld, 5052 or 6061?
5052 aluminum alloy has better welding performance and is suitable for projects that require a lot of welding. 6061 aluminum alloy may need heat treatment after welding to restore its mechanical properties.
Which aluminum alloy is more suitable for machining?
The machinability of 6061 aluminum alloy is better than 5052, and it is suitable for parts that require high-precision machining.
Is there a big price difference between these two aluminum alloys?
Generally speaking, 5052 aluminum alloy is cheaper and suitable for projects with limited budgets; 6061 aluminum alloy has a relatively high price due to its superior performance.
Please contact Huaxiao Metal for a price list of 5052 and 6061 aluminum. We have a wide range of thicknesses and conditions in stock for immediate shipment.
In Conclusion
The choice between 5052 aluminum and 6061 aluminum depends on your application requirements:
- Choose 5052 aluminum for superior corrosion resistance, high fatigue strength, and cost-effectiveness.
- When high strength, structural integrity, and machinability are critical, choose 6061 aluminum.
Still unsure? Contact Huaxiao Metal today for advice and competitive pricing on aluminum alloys.