Aluminum alloys are widely used in aerospace, automobile, construction, and other fields due to their lightweight, corrosion resistance, and good mechanical properties. Aluminum alloys are divided into several series according to their main alloying elements, among which 2000 aluminum vs. 7000 series aluminum alloys have attracted much attention due to their unique performance characteristics.
This article will explore the differences in the definition, performance, application, and cost of 2000 aluminum vs. 7000 series aluminum alloys to help readers better understand the advantages and applicable scenarios of these two types of aluminum alloys.
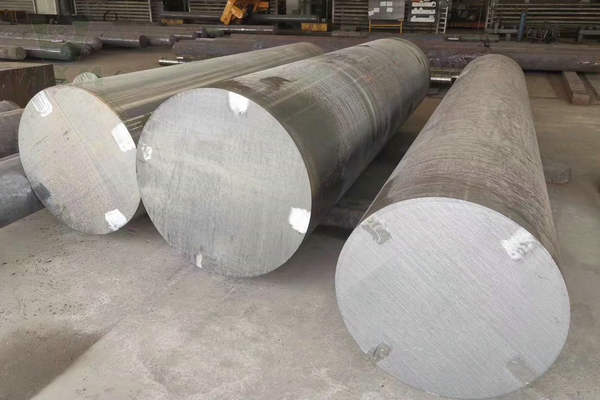
What is 2000 Series Aluminum?
The 2000 series aluminum alloy mainly uses copper (Cu) as the main alloying element, and usually also contains a small amount of magnesium (Mg), manganese (Mn) and other elements. This series of aluminum alloys has a high strength, close to or even exceeding the strength of some steels. The representative material of the 2000 series aluminum alloy is 2024 alloy, which is widely used in the aerospace field due to its good fatigue performance and high yield strength.
Looking for high-performance 2000 series aluminum alloys for your project?
Huaxiao Metal supplies top-grade 2000 series aluminum, including 2014, and 2024 aluminum alloys, etc., with excellent fatigue resistance and yield strength, ideal for aerospace and structural applications.
Get instant quotes and stock information for 2000 series aluminum.
What is 7000 Series Aluminum?
The 7000 series aluminum alloy mainly uses zinc (Zn) as the main alloying element, and usually adds elements such as magnesium (Mg) and copper (Cu) to further enhance its strength. 7075 alloy is a representative material in this series. It is widely used in aerospace, military equipment, and high-performance sports equipment due to its extremely high strength and good wear resistance.
Need ultra-high-strength aluminum for aerospace or performance-critical components?
Huaxiao Metal offers premium 7000 series aluminum alloys, including 7075 aluminum alloy, renowned for its exceptional strength and toughness. Request your 7000 series aluminum alloy quote today – get competitive pricing and fast delivery to meet your industrial needs.
2000 Aluminum VS. 7000 Aluminum Alloy:What's the Difference
Composition of 2000 Aluminum VS. 7000 Aluminum
2000 series: copper is the main alloying element, and the typical composition is aluminum-copper-magnesium alloy. Due to the addition of copper, this series of alloys has high strength, but also makes its corrosion resistance poor.
7000 series: zinc is the main alloying element, and usually also contains magnesium and copper. This series of alloys has higher strength due to the combination of zinc and magnesium, but its corrosion resistance is also relatively weak.
Performance of 2000 Aluminum VS. 7000 Aluminum
Strength: The strength of 7000 series aluminum alloys is generally higher than that of 2000 series, especially in 7075 alloys. The tensile strength of the 7075-T6 state can reach more than 500 MPa.
Corrosion Resistance: The corrosion resistance of 2000 series aluminum alloys is generally worse than that of 7000 series, especially in humid environments. However, corrosion resistance can be significantly improved by anodizing or coating.
Machinability: The machinability of 2000 series aluminum alloys is generally better than that of 7000 series, and is more suitable for the processing of complex parts. However, the 7000 series can also achieve good processing performance through an appropriate heat treatment process.
Application of 2000 Aluminum VS. 7000 Aluminum
2000 Series Aluminum Applications:
Aircraft structures
Automotive parts
Rivets and fasteners
Industrial equipment
7000 Series Aluminum Applications:
Airplane fuselage and wings
High-performance bicycle frames
Rock climbing gear
Robotics and military hardware
Not sure which series of aluminum alloys are right for your needs?
Contact us, Huaxiao Metal’s professional team can help you evaluate your project and recommend the right aluminum alloy.
Cost of 2000 vs 7000 Series Aluminum
The cost of 2000 series aluminum alloys is generally lower than that of 7000 series, partly because of their relatively simple alloy composition and relatively mature production process. The 7000 series is more expensive due to the addition of zinc and magnesium and a more complex heat treatment process.
Other Diferences of 2000 vs 7000 Series Aluminum Alloy
Heat Treatment Response
2000 series aluminum alloys: This series of aluminum alloys respond well to heat treatment (such as solution treatment, aging treatment, etc.). Through appropriate heat treatment processes, the strength of 2000 series aluminum alloys can be significantly improved. However, its aging hardening process is usually slow and it takes a long time to reach optimal performance.
7000 series aluminum alloys: 7000 series aluminum alloys are more sensitive to heat treatment, especially through the T6 heat treatment state, which can achieve high strength. This alloy has a fast heat treatment speed and can achieve a significant increase in strength in a short period. It is usually more suitable for industrial needs that require rapid mass production.
Fatigue Strength
2000 series aluminum alloys: 2000 series alloys have excellent fatigue strength, which makes them very suitable for use in structural parts that are subjected to repeated loads, especially in the aviation field. For example, 2024 alloy is often used in aircraft parts that need to withstand variable loads for a long time.
7000 series aluminum alloy: Although the static strength (tensile strength, yield strength) of the 7000 series is higher than that of the 2000 series, its fatigue strength is relatively low, especially in harsh environments. It is more sensitive to the extension of fatigue cracks, so some special structures may need to be strengthened to prevent fatigue failure.
Density
2000 series aluminum alloy: The density of the 2000 series aluminum alloy is about 2.78 g/cm³, which is slightly higher than that of conventional pure aluminum (about 2.7 g/cm³). Although its density does not change much, its strength-to-weight ratio (strength-to-weight ratio) is still relatively good, which is suitable for applications that need to reduce weight but have high strength requirements.
7000 series aluminum alloy: The density of the 7000 series is slightly higher, usually around 2.85–2.9 g/cm³. Despite the slight increase in density, due to its extremely high strength, the 7000 series still has advantages in high-strength, lightweight design, especially in aerospace and high-performance sports equipment.
Weldability
2000 Series Aluminum Alloys: The weldability of the 2000 series is poor, especially alloys with a high copper content. Cracks and defects are easily generated during welding, so special attention needs to be paid to the welding process, or other connection methods (such as riveting, bolting, etc.) are used.
7000 Series Aluminum Alloys: The weldability of the 7000 series aluminum alloys is also difficult, especially alloys with a high zinc content such as 7075, due to the tendency to thermal cracks. After welding, the mechanical properties of the material may also decrease, so mechanical connections or precision machining are often preferred rather than welding in high-strength applications.
Thermal Expansion Coefficient
2000 Series Aluminum Alloys: The thermal expansion coefficient of the 2000 series is relatively small, usually about 22.8 µm/m°C. This makes it have better dimensional stability in environments with large temperature fluctuations.
7000 Series Aluminum Alloys: The thermal expansion coefficient of the 7000 series aluminum alloy is higher, about 24 µm/m°C. In high-temperature environments, its dimensional changes may be greater than those of the 2000 series, which needs to be considered in the design.
Ductility
2000 series aluminum alloy: The ductility of 2000 series aluminum alloy is generally better than that of 7000 series, especially when it is not strengthened. It can be deformed more at a lower temperature and is not easy to crack during processing, so it is suitable for manufacturing parts with complex shapes.
7000 series aluminum alloy: The ductility of 7000 series aluminum alloy is relatively poor, especially in high high-strength state. Although this problem can be improved by appropriate processing technology, its use is limited in applications requiring large deformation.
Resistance to Stress Corrosion Cracking
2000 series aluminum alloy: The resistance of 2000 series aluminum alloy to stress corrosion cracking is generally poor, especially in high humidity or corrosive environments. Stress corrosion cracking is more likely to occur. To reduce such problems, it is usually necessary to treat it with anodizing or anti-corrosion coating.
7000 series aluminum alloy: The 7000 series aluminum alloy is very sensitive to stress corrosion cracking, especially in high-strength states (such as 7075-T6). Some new 7000 series alloys have improved stress corrosion resistance by adjusting the alloy element ratio and heat treatment process, such as newer alloys such as 7475.
How to Choose the Right Aluminum Alloy?
When making a choice, consider:
Strength Requirements → Go for the 7000 series for extreme load-bearing applications
Corrosion Environment → Use coatings or consider alternatives if long-term corrosion is a concern
Fatigue Performance → 2000 series is preferred in dynamic load environments
Cost and Machinability → 2000 series tends to be more cost-effective and easier to machine
Inquire Now for 2000 or 7000 aluminum alloy prices and stock availability.
In Conclusion
2000 series and 7000 series aluminum alloys each have their own advantages and application scenarios. 2000 series aluminum alloys are characterized by high strength, good fatigue performance and low cost, and are suitable for structural parts with low requirements for weight and corrosion resistance. 7000 series aluminum alloys are characterized by extremely high strength and good wear resistance, and are suitable for high-demand, high-performance occasions. The choice of which aluminum alloy should be based on the specific application requirements and economic costs.