Among the wide applications of aluminum alloys, 3003 aluminum vs 6061 aluminum are two materials that have attracted much attention. 3003 aluminum is famous for its excellent corrosion resistance and good forming performance, while 6061 aluminum has become the darling of the industry due to its high strength and versatility. Faced with various needs, how to choose the right material?
This article will compare these two aluminum materials in detail from the aspects of chemical composition, mechanical properties, physical properties, price, application, etc., to help you make the right choice.
If you have any purchasing needs, please feel free to contact Huaxiao Metal to get the latest quotes for 3003 aluminum alloy and 6061 aluminum alloy!
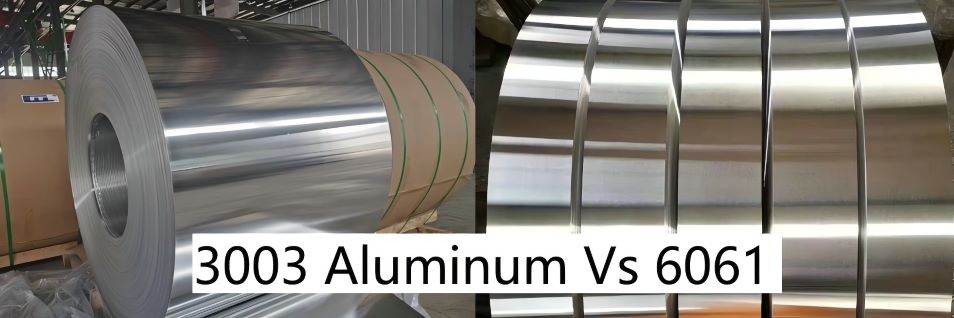
What is 3003 Aluminum Alloy?
3003 aluminum is an aluminum-manganese alloy, which belongs to the typical rust-proof aluminum alloy series. It contains about 1.2% manganese, which gives it good corrosion resistance and certain strength. It is light in weight and has excellent machinability, especially suitable for cold cold-forming process. It is an economical and general aluminum.
Common Temper:
H14: Improved strength through cold working, with medium hardness and good corrosion resistance.
Features of 3003 Aluminum:
- Excellent oxidation resistance and rust resistance
- Easy to bend and weld
- Smooth surface, suitable for decorative purposes
What is 6061 Aluminum Alloy?
6061 aluminum is an aluminum-magnesium-silicon alloy known for its high strength, good mechanical properties and welding performance. It can significantly improve its hardness and strength through heat treatment while maintaining good corrosion resistance. It is a high-performance aluminum material suitable for a variety of complex industrial needs.
Common Temper of 6061 Aluminum:
T6: After solution heat treatment and natural aging, it has extremely high strength and hardness, suitable for load-bearing structures and demanding industrial applications.
Features of 6061 Aluminum:
- High strength and good processability
- Excellent welding performance, not easy to crack after welding
- Diverse surface treatments, suitable for anodizing and coating
3003 Aluminum Vs 6061: What’s the Difference?
Composition of 3003 Aluminum Vs 6061:
Element | 3003 Aluminum | 6061 Aluminum |
---|---|---|
Al | 96.8% – 99% | 95.8% – 98.6% |
Mn | 1.0% – 1.5% | Max 0.15% |
Mg | Max 0.05% | 0.8% – 1.2% |
Si | Max 0.6% | 0.4% – 0.8% |
Cu | Max 0.2% | 0.15% – 0.40% |
Cr | — | 0.04% – 0.35% |
Fe | Max 0.7% | Max 0.7% |
3003 aluminum alloy is a typical manganese alloy with good anti-rust ability, while 6061 aluminum alloy belongs to aluminum-magnesium-silicon heat-treatable alloy with excellent comprehensive performance and can be strengthened by T6 heat treatment.
Mechanical Properties: Aluminum 3003 vs. 6061
Property | 3003 H14 | 3003 H12 | 3003 H16 | 3003 H18 | 6061 T6 | 6061 T4 | 6061 T5 | 6061 O |
---|---|---|---|---|---|---|---|---|
Ultimate Tensile Strength (UTS) | 145 – 195 MPa | 135 – 175 MPa | 160 – 200 MPa | 170 – 210 MPa | 290 – 310 MPa | 180 – 250 MPa | 250 – 300 MPa | 130 – 180 MPa |
Yield Strength | 120 MPa | 110 MPa | 130 MPa | 150 MPa | 240 MPa | 140 – 210 MPa | 210 – 260 MPa | 45 – 75 MPa |
Elongation | 10% – 15% | 15% – 20% | 5% – 10% | 3% – 5% | 8% – 12% | 15% – 18% | 12% – 15% | 25% – 30% |
Brinell Hardness | ~45 HB | ~45 HB | ~50 HB | ~55 HB | ~95 HB | ~60 – 75 HB | ~75 – 85 HB | ~25 – 40 HB |
Modulus of Elasticity | 68.9 GPa | 68.9 GPa | 68.9 GPa | 68.9 GPa | 68.9 GPa | 68.9 GPa | 68.9 GPa | 68.9 GPa |
It can be seen that the 6061 aluminum alloy is significantly better than the 3003 aluminum alloy in terms of strength and hardness, so 6061 is more suitable for situations that require load-bearing or structural support. 3003 has more advantages in formability and ductility and is suitable for deep drawing and stretching processes.
Physical Properties Comparison: Aluminum 3003 vs. 6061
Property | 3003 Aluminum | 6061 Aluminum |
---|---|---|
Density | 2.73 g/cm³ | 2.70 g/cm³ |
Thermal Conductivity | 222 W/m·K | 167 W/m·K |
Melting Point | 643 – 654°C | 582 – 652°C |
Corrosion Resistance | Excellent | Good |
Electrical Conductivity | 41% IACS | 43% IACS |
Cost of 3003 Aluminum Vs 6061:
3003 aluminum is cheaper than 6061.
3003 aluminum is relatively cheap in the market due to its low production cost, making it an economical choice.
6061 aluminum is relatively more expensive due to its stronger comprehensive performance, but its high strength and versatility bring higher cost performance.
Want to know the real-time price of 3003 aluminum alloy and 6061 aluminum alloy? Feel free to contact Huaxiao Metal to get aluminum prices and inventory information now!
Weldability and Processability of 3003 Aluminum Vs 6061:
3003 aluminum alloy has excellent welding performance and cold forming performance, is suitable for welding using traditional welding techniques (such as TIG, MIG), and has good connection performance under low strength requirements.
6061 aluminum alloy has good welding performance but requires heat treatment or aging after welding to restore strength. Welding in the T6 state will soften and should be used with caution.
If your project requires complex bending, stamping, or welding processes, Huaxiao Metal recommends using 3003 aluminum; if you have higher requirements for strength and rigidity, you should choose 6061 aluminum.
Corrosion Resistanceof 3003 Aluminum Vs 6061:
Due to its manganese content, 3003 aluminum alloy has good corrosion resistance and is suitable for corrosion-sensitive environments such as food, the chemical industry, and interior decoration.
Although 6061 aluminum alloy also has good oxidation resistance, its corrosion resistance is slightly inferior to 3003, especially in welded parts.
If your use scenario is in a humid, high-humidity, or chemical environment, it is recommended to give priority to the 3003 aluminum sheet.
Application of 3003 Aluminum Vs 6061:
3003 Aluminum:
Suitable for scenes with high requirements for corrosion resistance, such as:
- Food packaging (beverage cans, canned containers)
- Chemical storage tanks
- Roofing materials, wall panels
- Household appliance parts
6061 Aluminum:
Suitable for scenes with high strength and complex processing requirements, such as:
- Building frames and supports
- Ship parts and automotive parts
- Aerospace equipment
- Mold manufacturing
Aluminum 3003 h14 vs 6061 t6:
3003 H14: Moderate hardness, good oxidation resistance, rust resistance, easy to cold work.
6061 T6: Significantly improved hardness and strength, suitable for load-bearing structures, but more difficult to cold work.
Conclusion: Which Is the Better Choice?
Whether to choose 3003 aluminum or 6061 aluminum depends on your specific needs:
Scenarios for choosing 3003 aluminum:
If the project requires high corrosion resistance, economy, and easy-to-form materials, 3003 aluminum is the best choice.
Typical industries: food processing, building decoration, chemical storage tanks.
Scenario for choosing 6061 aluminum:
If the project has high requirements for strength, hardness, and versatility, 6061 aluminum is more suitable.
Typical industries: aerospace, automotive industry, mechanical equipment.
Whether you choose 3003 aluminum vs 6061 aluminum, they can show excellent performance in different fields.
Huaxiao Metal provides high-quality 3003 aluminum (H14 state) and 6061 aluminum (T6 state), with sufficient stock and favorable prices. Feel free to contact us for professional material selection suggestions and the latest quotes!