7075 refers to a common alloy in the 7000 series aluminum alloy. It is a cold-processed forging alloy with high strength, far exceeding that of mild steel.
7075 is one of the most powerful alloys in commercial use, with a tight structure and strong corrosion resistance, such as aviation and marine plates. It also has corrosion resistance, mechanical properties and anodic reaction.
What is 7075 Aluminum?
A type of aluminum alloy, 7075 is aviation aluminum, belonging to the Al-Zn-Mg-Cu series of super-hard aluminum. Among the more common aluminum alloys, 7075 alloy has the best strength, but it cannot be welded, and its corrosion resistance is quite poor. Many CNC cutting parts use 7075 alloys. Zinc is the main alloying element in this series, and adding a little magnesium alloy can make the material heat-treated and reach very high strength characteristics.
This series of materials generally adds a small amount of copper, chromium, and other alloys. The 7075 aluminum alloy is particularly top-grade, with the highest strength, suitable for aircraft frames and high-strength accessories.
7075 Aluminium Alloy
The Characteristics of 7075 Aluminum Plate
7075 aluminum plate is a cold-treated forged alloy with high strength and hardness, far superior to mild steel. 7075 aluminum plate is one of the strongest commercial alloys, with general corrosion resistance, good mechanical properties and anodic reaction. The fine grains make deep drilling performance better, tool wear resistance enhanced, thread rolling more different, when the density requirement is small, the preferred metal material with high hardness requirement.
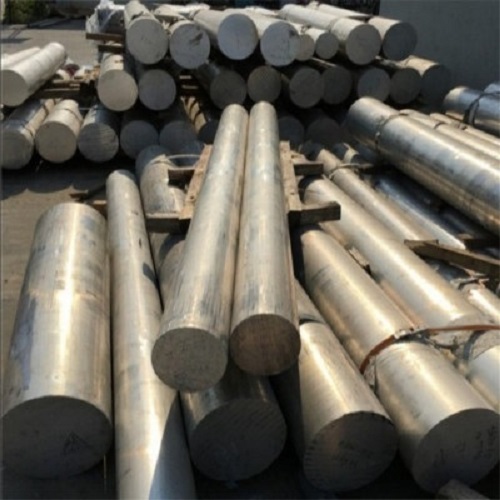
7075 is an aluminum alloy with zinc as the main alloying element, but sometimes magnesium and copper are added in small amounts. Among them, super-hard aluminum alloy is an alloy containing zinc, lead, magnesium and copper, which is close to the hardness of steel, can be strengthened by heat treatment, is a high-strength, heat-treatable alloy, has ordinary corrosion resistance and good mechanical properties. Aluminum 7075 is a cold-treated forged alloy with high strength, far superior to mild steel.
7075 aluminum alloy is one of the strongest commercial alloys. Ordinary corrosion resistance, good mechanical properties, and anodic reaction. The fine grains make deep drilling performance better, tool wear resistance enhanced, and thread rolling more different.
Common types of aluminum plates and aluminum alloys include aluminum strips, aluminum foils, aluminum plates, aluminum tubes, mirror aluminum plates, alloy aluminum plates, curtain wall aluminum plates, patterned aluminum plates, embossed aluminum plates, aluminum rods, non-slip aluminum plates, anodized aluminum plates, cold-rolled aluminum plates, hot-rolled aluminum plates, southwest plates (imported), mirror aluminum plates, pure aluminum plates, pure aluminum coils, deep-drawn aluminum plates, lighting aluminum plates, bottle cap materials, circuit boards, transformer-specific aluminum strips, aluminum foils, composite bottom plates, rust-proof aluminum plates, etc.
Used to manufacture aircraft structures and other high-stress structural parts that require high strength and strong corrosion resistance, such as upper and lower wing panels, girders, bulkheads, etc. After solution treatment, the plasticity is good, and the heat treatment strengthening effect is particularly good. It has high strength below 150°C and has particularly good low-temperature strength, poor welding performance, and a tendency to stress corrosion cracking. Double-stage aging can improve SCC resistance. Provided by Wuxi Hanshin Metallurgy.
What is 7075-T6?
Introduction to 7075 Aluminum Alloy
7075 aluminum alloy is one of the strongest commercial aluminum alloys, usually called “hard aluminum”, and its hardness is better than mild steel. As a representative of the 7 series aluminum-zinc-magnesium aluminum alloy, the advantages of 7075 are excellent mechanical properties and good anodic reaction. Its disadvantages are poor welding performance and a tendency to stress corrosion.
Uses of 7075
7075 is often used in the aviation and mold fields. For aircraft parts that require both strength and lightness, 7075 is the best choice; in the mold field, it has a hardness comparable to steel, excellent thermal and electrical conductivity, and better machining performance. 7075 is a good substitute for alloy steel. In addition, 7075 is also used to make golf heads.
What is 7075-T651?
Introduction to 7075 -T651
HXM has a large number of 7075-T651 aluminum for sale, providing new quotes for 7075-T651 aluminum prices. Online customer service professionally answers questions about the relevant performance parameters of 7075-T651 aluminum, the density of 7075-T651 aluminum, what material 7075-T651 is made of, what material 7075-T651 is made of, and how much 7075-T651 aluminum costs per kilogram. Regarding the welding process of 7075-T651 aluminum, our online customer service will also answer your questions. Friends who need to order 7075-T651 aluminum are welcome to call for a consultation.
7075-T651 aluminum plate is known as an excellent product among aluminum alloys. T651 means that the alloy has undergone heat treatment and a pre-stretching process. The tensile strength of T6 and T651 alloys is 572MPa and the yield strength is 503MPa. At the same time, 7075 alloy has good mechanical properties and anodizing properties. The ASTM Standards Alliance rates 7075 alloys as having Grade B mechanical properties because of their ability to produce curled or brittle chips with an excellent surface finish.
7075-T651 Mechanical Properties
Thermal expansion coefficient (20-100 ° C) um / m.k: 23.6, 7075-T651 aluminum melting point range (℃): 475-635, conductivity 20 ° C (68 ° F) (% ACS): 33, 7075-T651 aluminum resistivity 20 ° C (68 ° F) m ㎡ / m: 0.0515.
Aluminum and aluminum alloys can dissolve a large amount of hydrogen in the liquid state and almost no hydrogen in the solid state. In the process of welding molten pool solidification and rapid cooling, hydrogen is too late to overflow, it is very easy to form hydrogen pores. Moisture in the arc column atmosphere, moisture adsorbed by the oxide film on the surface of the welding material, and the base material are important sources of hydrogen in the weld. Therefore, the source of hydrogen should be strictly controlled to prevent the formation of porosity.
Alloying elements are easy to evaporate and burn so that the performance of the weld decreases.
Aluminum is a face-centered cubic lattice, there are no allotropic isomers, there is no phase transition during heating and cooling, weld grain is easy to coarsen, and can not be refined through the phase transition to grain.
Welding Methods
In welding methods, almost all kinds of welding methods can be used for welding aluminum and aluminum alloy, but aluminum and aluminum alloy on the adaptability of various welding methods are different, and a variety of welding methods have their applications. Gas welding and electrode arc welding methods, simple equipment, and easy to operate. Gas welding can be used for welding quality.
Requirements for welding quality are not high aluminum sheet and castings of the complementary welding. Electrode arc welding can be used for aluminum alloy castings. The inert gas shielded welding (TIG or MIG) method is a widely used aluminum and aluminum alloy welding method. Aluminum and aluminum alloy thin plates can be used in tungsten exchange argon arc welding or tungsten pulse argon arc welding.
Aluminum and aluminum alloy thick plates can be used for tungsten helium arc welding, argon-helium mixed tungsten gas-shielded welding, fusion electrode gas-shielded welding, and pulse fusion electrode gas-shielded welding. The application of fusion electrode gas-shielded welding and pulsed fusion electrode gas-shielded welding is becoming increasingly widespread (argon or argon-helium mixed gas).
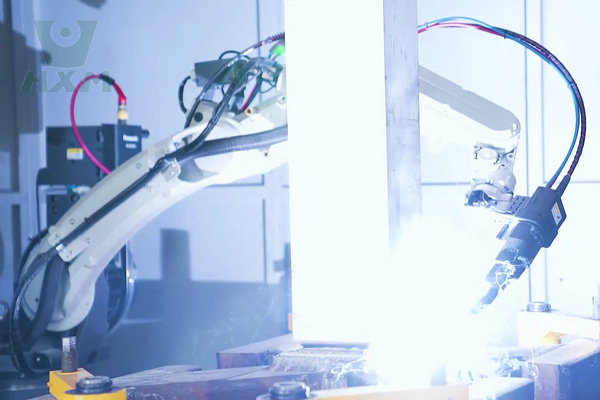