ALUMINUM Metal | ALUMINUM SUPPLIER
HXM Metal is a national aluminum metal supplier that frequently stocks aluminum sheets and bars. We also sell aluminum wires, tubes, coils, strips, channels, angles, custom extruded profiles, and more.
At HXM, we focus on product quality and customer experience. Our professional team is ready to provide technical support and consulting services to help you choose the aluminum metal product that best suits your needs. We also regularly track aluminum metal market trends to provide customers with the latest price information and market trend analysis to help them make informed decisions.
If you are looking for a reliable aluminum metal supplier and partner, HXM will be your best choice. Contact us and let us work together to create a better future!
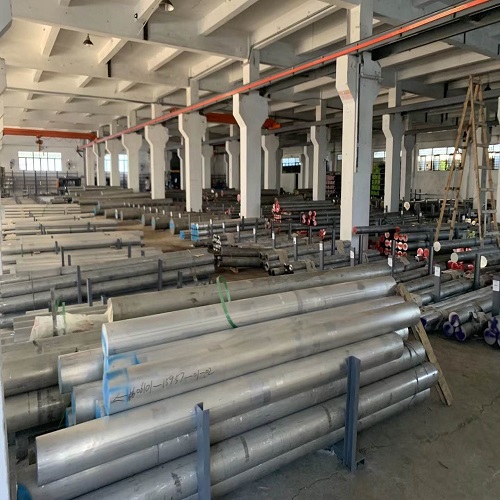
Learn More About Each Type of Aluminum Supplier Format
Our company provides aluminum metal products in various forms, including plates, bars, tubes, and wires. Our aluminum plates are suitable for the construction, aerospace, and automotive industries, providing lightweight and high-strength solutions. Profiles are widely used in doors and windows, car bodies and mechanical components, with good processability and excellent strength-to-weight ratio.
More Details About Each Aluminum Metal Grade
Our company offers a variety of aluminum metal products, including 1000 series to 8000 series. These series cover a variety of aluminum alloy types, suitable for a variety of applications. Our products include aluminum metal sheets, profiles, tubes, and castings to meet your needs for lightweight, high strength and corrosion resistance.
1000 series aluminum alloy is a very common type of aluminum alloy. Its main component is pure aluminum and usually contains small amounts of other elements, such as iron, copper, manganese, silicon, etc. These alloys are widely used in a variety of applications due to their excellent processability, electrical conductivity, and corrosion resistance.
If you would like to learn more about 1000 series aluminum products, please click here. If you want to purchase 1000 series aluminum products directly, please send us your inquiry directly!
2000 series aluminum alloy is a type of high-strength aluminum alloy whose main alloying element is copper. These alloys have excellent mechanical properties, especially under high temperature conditions, and are therefore widely used in aerospace, defense and other fields.
If you want to know more about 2000 series aluminum products, please click here. If you want to purchase 2000 series aluminum products directly, please send us your inquiry directly!
3000 series aluminum alloy is a type of aluminum alloy containing manganese as the main alloying element. These alloys generally have good corrosion resistance and formability, making them suitable for a variety of applications requiring corrosion resistance.
If you want to know more about 3000 series aluminum products, please click here. If you want to purchase 3000 series aluminum products directly, please send us your inquiry directly!
4000 series aluminum alloy is a type of aluminum alloy containing silicon as the main alloying element. These alloys generally have good weldability and corrosion resistance and are suitable for applications requiring high welding performance.
If you want to know more about 4000 series aluminum products, please click here. If you want to purchase 4000 series aluminum products directly, please send us your inquiry directly!
5000 series aluminum alloys are a class of aluminum alloys containing magnesium as the main alloying element. These alloys generally have good corrosion resistance and strength and are suitable for a variety of applications requiring high strength and corrosion resistance.
If you want to learn more about 5000 series aluminum products, please click here. If you want to purchase 5000 series aluminum products directly, please send us your inquiry directly!
6000 series aluminum alloy is a common type of aluminum alloy whose main alloying elements are silicon and magnesium. These alloys generally have good mechanical properties, processability and corrosion resistance and are widely used in various industrial fields.
If you want to learn more about 6000 series aluminum products, please click here. If you want to purchase 6000 series aluminum products directly, please send us your inquiry directly!
The 7000 series aluminum alloy is a type of high-strength aluminum alloy whose main alloying element is zinc and also contains smaller amounts of copper and magnesium. These alloys often have excellent mechanical properties, particularly in applications with high strength requirements.
If you want to know more about 7000 series aluminum products, please click here. If you want to purchase 7000 series aluminum products directly, please send us your inquiry directly!
8000 series aluminum alloys are a group of aluminum alloy materials with excellent properties and a wide range of applications. These alloys usually exist in the form of a mixture of aluminum and other elements, such as copper, zinc, manganese and magnesium. 8000 series aluminum alloys have high strength, good corrosion resistance and excellent processability, and are suitable for a variety of industrial and engineering fields. They are often used in aerospace, automotive manufacturing, construction and electronic equipment, and are favored for their advantages such as light weight, high strength and corrosion resistance.
In general, 8000 series aluminum alloys provide reliable material solutions for a variety of applications. If you need 8000 series aluminum, please contact us directly!
Frequently Asked Questions
Galvanized Metal vs Aluminum
Galvanized metal and aluminum are two common metal materials that have different characteristics and uses in their respective fields.
Galvanized metal refers to the coating of the surface of iron or steel with a layer of zinc to prevent it from oxidation and corrosion. Galvanized metal is often used in outdoor structures and buildings, such as roofs, railings, pipes, etc., and is favored for its good weather resistance and corrosion resistance.
Aluminum is a lightweight, corrosion-resistant metal material that is often used in the manufacture of aircraft, automobiles, ships and other products that require lightweight and high strength. The advantages of aluminum are its light weight, good conductivity and resistance to corrosion, so it is widely used in many industrial and aviation fields.
In general, galvanized metal is suitable for occasions that require corrosion resistance, while aluminum is suitable for occasions that require light weight, high strength and conductivity. Which material to choose depends on the specific application requirements and environmental conditions.
Magnesium Alloy vs Aluminum
Lightweight:
- Magnesium Alloy: Magnesium alloy is the lightest of all lightweight metals, even lighter than aluminum alloy.
- Aluminum Alloy: Aluminum alloy is also lightweight but slightly heavier compared to magnesium alloy.
Strength:
- Magnesium Alloy: Magnesium alloy generally has lower strength, but it can be enhanced through appropriate alloying and heat treatment.
- Aluminum Alloy: Aluminum alloy has higher strength, especially after suitable heat treatment.
Corrosion Resistance:
- Magnesium Alloy: Magnesium alloy has relatively poor corrosion resistance, being less resistant to oxidation and corrosion.
- Aluminum Alloy: Aluminum alloy exhibits better corrosion resistance, particularly against oxidation.
Processability:
- Magnesium Alloy: Magnesium alloy has good processability and is easily cast and formed.
- Aluminum Alloy: Aluminum alloy also boasts good processability and is widely used in various processing techniques.
Applications:
- Magnesium Alloy: Commonly used in automotive and aerospace industries to reduce structural weight and improve fuel efficiency. Also utilized in electronics and sporting goods.
- Aluminum Alloy: Widely employed in construction, aerospace, automotive, electronics, and various other industries due to its excellent strength-to-weight ratio, good processability, and corrosion resistance.
In summary, both magnesium alloy and aluminum alloy are significant lightweight metal materials, each with its own advantages and applications. When selecting a material, specific application requirements, strength demands, and environmental conditions need to be considered.
Aluminum Alloy vs Stainless Steel
Material Composition:
- Aluminum Alloy: Aluminum alloy is primarily composed of aluminum, with other elements such as copper, magnesium, zinc, or silicon added to enhance its properties.
- Stainless Steel: Stainless steel is an alloy composed mainly of iron, with a minimum of 10.5% chromium content and other elements like nickel, manganese, or molybdenum to provide corrosion resistance and other properties.
Corrosion Resistance:
- Aluminum Alloy: Aluminum alloy has natural corrosion resistance due to its oxide layer, but it can corrode in certain environments, particularly in acidic or alkaline conditions.
- Stainless Steel: Stainless steel is highly resistant to corrosion, especially in harsh environments, making it suitable for applications where corrosion resistance is crucial.
Strength:
- Aluminum Alloy: Aluminum alloy typically has lower strength compared to stainless steel, but it can be strengthened through various alloying and heat treatment processes.
- Stainless Steel: Stainless steel generally has higher strength compared to aluminum alloys, particularly in terms of tensile and yield strength.
Weight:
- Aluminum Alloy: Aluminum alloy is lightweight, with a density about one-third that of steel, making it advantageous for weight-sensitive applications.
- Stainless Steel: Stainless steel is denser and heavier compared to aluminum alloy, which can be a disadvantage in weight-critical applications.
Cost:
- Aluminum Alloy: Aluminum alloy is typically less expensive than stainless steel, making it a cost-effective choice for certain applications.
- Stainless Steel: Stainless steel tends to be more expensive due to its higher material costs and manufacturing processes, but it offers long-term durability and corrosion resistance.
Appearance:
- Aluminum Alloy: Aluminum alloy has a shiny appearance and can be anodized or coated with various finishes for aesthetic appeal.
- Stainless Steel: Stainless steel has a distinctive silver-gray color and a smooth, polished surface, which can enhance the visual appeal of products.
In summary, both aluminum alloy and stainless steel have unique properties and advantages, making them suitable for different applications. The choice between the two depends on factors such as corrosion resistance requirements, strength needs, weight considerations, cost constraints, and aesthetic preferences.
Titanium Metal vs Aluminum
Material Composition:
- Titanium: Titanium is a chemical element with the symbol Ti and atomic number 22. It is a transition metal known for its excellent strength-to-weight ratio and corrosion resistance.
- Aluminum: Aluminum is a chemical element with the symbol Al and atomic number 13. It is a lightweight metal known for its low density and corrosion resistance.
Strength:
- Titanium: Titanium is renowned for its high strength-to-weight ratio, making it exceptionally strong for its relatively low density. It is stronger than aluminum, especially in terms of tensile strength.
- Aluminum: Aluminum is also strong, but its strength is generally lower compared to titanium. However, aluminum alloys can be tailored to enhance specific mechanical properties.
Density:
- Titanium: Titanium is denser than aluminum, with a density of approximately 4.5 g/cm³.
- Aluminum: Aluminum is lightweight, with a density of about 2.7 g/cm³, making it significantly lighter than titanium.
Corrosion Resistance:
- Titanium: Titanium exhibits excellent corrosion resistance, especially in harsh environments such as seawater and chemical processing. It forms a protective oxide layer that prevents further corrosion.
- Aluminum: Aluminum also has good corrosion resistance due to the formation of a thin oxide layer on its surface. However, it is not as corrosion-resistant as titanium in certain aggressive environments.
Cost:
- Titanium: Titanium is more expensive than aluminum, both in terms of material cost and processing. Its higher cost is primarily due to its scarcity and the complex extraction and refinement process.
- Aluminum: Aluminum is relatively inexpensive compared to titanium, making it a more cost-effective choice for many applications.
Applications:
- Titanium: Titanium is commonly used in aerospace, military, medical implants, and high-performance sports equipment where its combination of strength, lightness, and corrosion resistance is essential.
- Aluminum: Aluminum finds widespread use in aerospace, automotive, construction, packaging, and consumer goods due to its lightweight nature, ease of fabrication, and corrosion resistance.
In summary, both titanium and aluminum offer unique advantages and are suitable for various applications. Titanium excels in applications where high strength, lightness, and corrosion resistance are paramount, albeit at a higher cost. Aluminum, on the other hand, provides a cost-effective solution for lightweight structures with good corrosion resistance. The choice between the two depends on specific application requirements, budget considerations, and other factors.
Looking forward to being your Aluminum Metal choice!